Transforming Artistic Innovation and Manufacturing Excellence: The Future of Art Supplies, Product Design, and 3D Printing at arti90.com
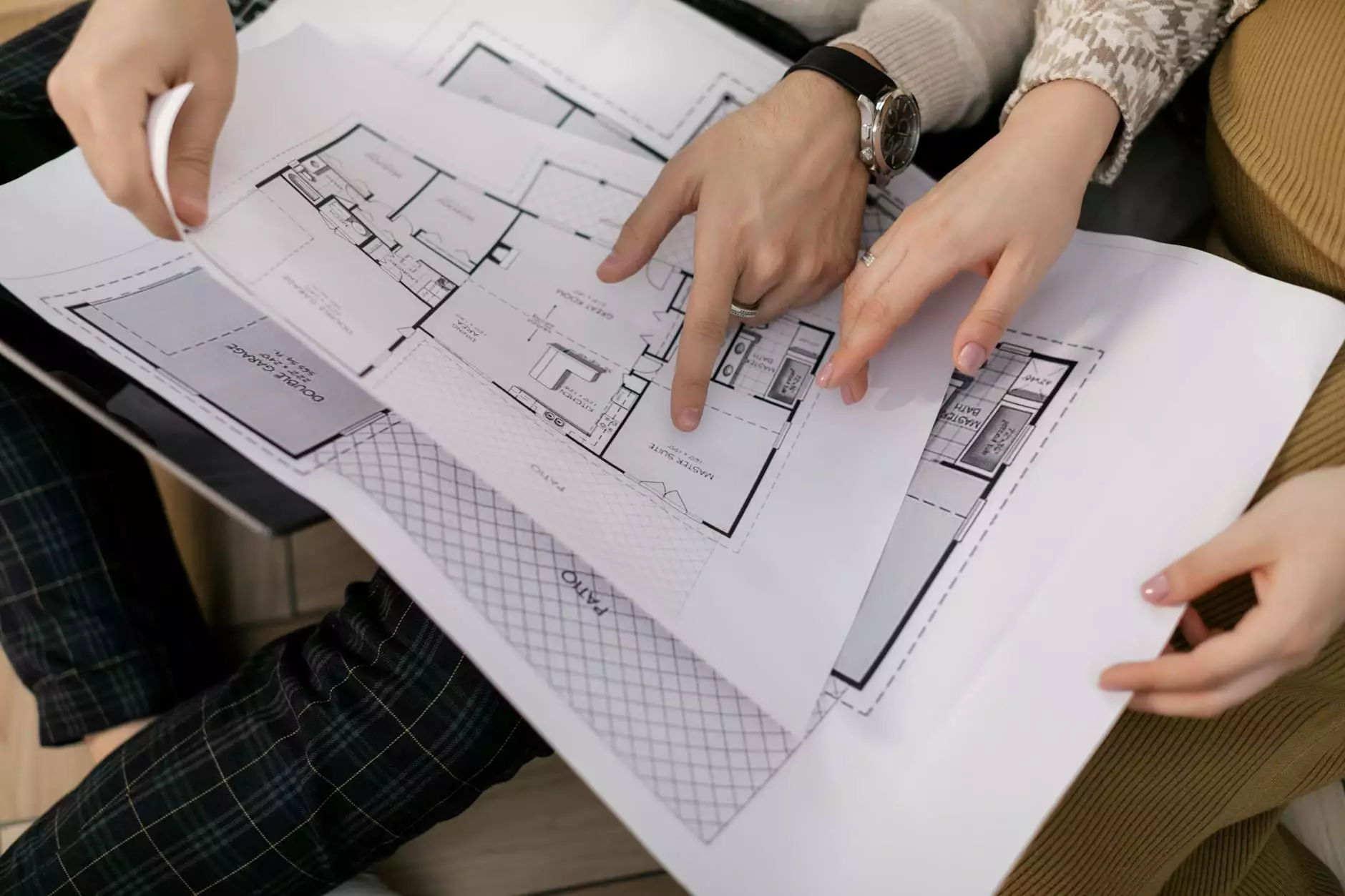
In today's rapidly evolving marketplace, businesses operating in the domains of art supplies, product design, and 3D printing are redefining the boundaries of creativity and manufacturing efficiency. Leveraging cutting-edge technologies such as the low pressure casting process, companies like arti90.com are pioneering new ways to produce high-quality, durable, and innovative products that meet the demands of modern artists, designers, and manufacturers.
Understanding the Dynamic Landscape of Art Supplies and Creative Tools
The art supplies industry has long been the backbone of creative expression. From traditional pencils and paints to sophisticated digital tools, this sector continues to evolve swiftly. Today, consumers demand more than just basic materials—they seek products that inspire, enhance, and facilitate their artistic journey. Companies investing in research and development are introducing technologically advanced supplies such as eco-friendly materials, ergonomic tools, and precision instruments designed for both amateurs and professionals.
Key trends shaping the art supplies sector include:
- Sustainable and eco-friendly materials: Growing emphasis on environmentally conscious manufacturing.
- Technological integration: Incorporating apps, smart tools, and digital interfaces for a seamless creative process.
- Customization and personalization: Products tailored to individual preferences through innovative manufacturing techniques.
Advancement in manufacturing methods, like the low pressure casting process, plays a pivotal role in enabling the creation of intricate, high-quality art supplies that stand out in the marketplace.
Innovations in Product Design for Next-Generation Creativity
Product design is the heart of innovation in the creative industries. It encompasses not only aesthetic appeal but also functionality, ergonomics, and durability. Today's designers are leveraging digital tools such as CAD (Computer-Aided Design), 3D modeling, and simulation to develop products that are both beautiful and highly practical.
By integrating advanced manufacturing processes, including low pressure casting process, designers can turn prototypes into production-ready items with remarkable precision. This process allows for complex geometries and detailed structures, making it ideal for creating unique art supplies, custom jewelry, and industrial design prototypes.
Benefits of modern product design include:
- Enhanced precision and detail: Achieved through digital design and manufacturing integration.
- Reduced lead times: Rapid prototyping with 3D printing and casting techniques expedites product development.
- Sustainable manufacturing: Utilizing eco-friendly materials and processes to reduce waste.
- Mass customization: Catering to individual preferences with minimal additional costs.
At arti90.com, the commitment to innovative product design supported by low pressure casting process signifies a strategic advantage in delivering bespoke art and design solutions that surpass customer expectations.
The Revolutionary Role of 3D Printing in Modern Manufacturing
3D printing has transformed the landscape of manufacturing, enabling rapid prototyping, complex geometries, and even small-scale production runs that were previously impossible or prohibitively expensive. This technology empowers artists, designers, and engineers to explore new creative avenues and produce highly customized components with unparalleled precision.
The integration of 3D printing with traditional manufacturing methods enhances flexibility and reduces costs, especially for intricate or bespoke items. At arti90.com, 3D printing is seamlessly integrated with techniques like low pressure casting process to optimize production efficiency and quality.
Key advantages of 3D printing include:
- Rapid iteration: Quickly modifies designs and tests prototypes.
- Complex geometries: Produces intricate structures that traditional methods can't support.
- Cost-effective small batch production: Eliminates the need for expensive molds or tooling.
- Material versatility: Supports a wide range of materials including plastics, resins, and metals.
Blending 3D printing with the low pressure casting process unlocks new dimensions in product development, offering unmatched detail and strength for both artistic and industrial applications.
How the Low Pressure Casting Process Reinforces Industry Innovation
The low pressure casting process is a sophisticated manufacturing technique that enables the production of high-quality metal and alloy components with remarkable precision. Unlike traditional gravity casting, this process applies controlled, low-pressure air or inert gases to fill molds with molten metal, ensuring uniform flow and minimizing air entrapment or defects.
This method is particularly advantageous for producing detailed, complex castings needed in artistic sculptures, jewelry, and customized industrial parts. It offers several benefits over traditional casting techniques, including:
- Exceptional surface finish and detail: Ideal for intricate artistic designs and high-precision parts.
- Reduced porosity and defects: Controlled pressure results in denser, more durable castings.
- Consistency and repeatability: Ensures uniform quality across production runs.
- Material efficiency: Minimized waste and improved use of costly alloys.
By incorporating low pressure casting process into its manufacturing pipeline, arti90.com can produce superior art supplies, custom sculptures, and design prototypes that meet the highest standards of quality and craftsmanship.
The Synergy of Technology and Business Strategy at arti90.com
arti90.com exemplifies how embracing innovative manufacturing techniques, such as the low pressure casting process, can be a game-changer for business growth. Their strategic focus on integrating art supplies, product design, and 3D printing creates a comprehensive ecosystem that supports artists, designers, and industrial clients alike.
Key strategies for business success include:
- Investing in R&D: Continuously exploring new materials, processes, and designs.
- Adopting cutting-edge technologies: Using 3D printing and low pressure casting process for product excellence.
- Fostering innovation and customization: Streamlining personalized offerings to stand out in the market.
- Building strong supplier and partner relationships: Ensuring access to quality materials and advanced machinery.
This strategic approach positions arti90.com at the forefront of the creative manufacturing industry, ensuring sustainable growth and increased market share.
Future Outlook: Redefining Creative Industries with Advanced Manufacturing
The future of the art supplies, product design, and 3D printing industries depends heavily on innovative manufacturing techniques like the low pressure casting process, which offers unparalleled precision, efficiency, and customization.
Emerging trends point toward a more integrated, smart manufacturing ecosystem that leverages artificial intelligence, IoT, and automation to optimize production cycles and quality control further.
By staying ahead of these advancements, companies like arti90.com will continue to drive industry standards, delivering products that are not only aesthetically pleasing but also maximally functional and sustainable.
Conclusion: Embracing Innovation to Secure a Competitive Edge
In conclusion, the intersection of innovative business strategies, cutting-edge manufacturing processes like the low pressure casting process, and a strong focus on art supplies, product design, and 3D printing defines the future landscape of creative industries. arti90.com epitomizes this synergy, demonstrating how technological excellence and visionary business acumen create unmatched opportunities for growth and success.
Businesses that prioritize research, embrace technological advancements, and foster a culture of innovation will thrive in an increasingly competitive marketplace. With continuous investment in such transformative tools and processes, they are well-positioned to lead the way in redefining art, design, and manufacturing for decades to come.
Now more than ever, embracing the low pressure casting process and synergizing it with digital manufacturing technologies is essential for unlocking new potentials in the art and industrial sectors.