The Advantages and Applications of Low Pressure Casting in Business
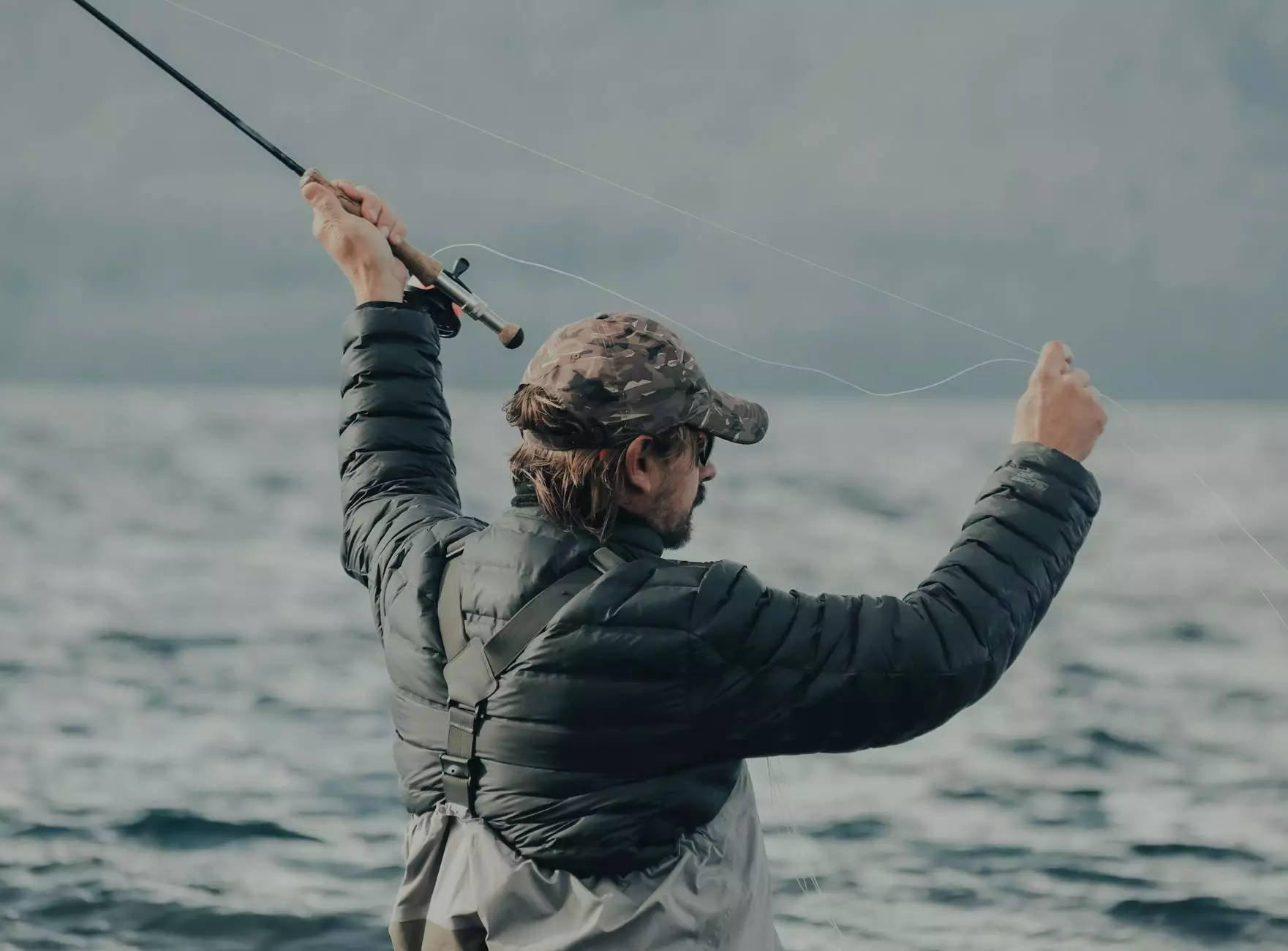
Low pressure casting is an innovative manufacturing technique that has gained significant traction across various industries, including art supplies, product design, and 3D printing. This method offers a plethora of benefits, such as improved product quality, reduced waste, and enhanced design flexibility. In this article, we will delve into what low pressure casting is, its advantages, and its potential applications across different sectors.
Understanding Low Pressure Casting
Low pressure casting, often referred to as low pressure die casting or LPDC, is a process characterized by the use of atmospheric pressure to fill a mold with liquid metal. Unlike traditional casting methods, which often rely on gravitational forces, LPDC operates at low pressures, typically around 1-2 bar. This process not only minimizes turbulence during metal filling but also ensures better mold filling, leading to enhanced precision and reduced defects.
How Does Low Pressure Casting Work?
The low pressure casting process involves several key steps:
- Mold Preparation: Molds are engineered to precise specifications, often made from steel or other durable materials resistant to high temperatures.
- Metal Melting: The metal is melted in a furnace, achieving a temperature that ensures fluidity.
- Low Pressure Filling: The molten metal is introduced into the mold under low atmospheric pressure, allowing for even distribution without the risk of air entrapment.
- Cooling and Solidification: The metal cools and solidifies within the mold, taking its desired shape.
- Mold Removal and Finishing: Once cooled, the mold is removed, and any finishing processes—such as machining or polishing—are applied.
Benefits of Low Pressure Casting
Enhanced Product Quality
One of the most significant advantages of low pressure casting is the enhanced quality of the finished products. The controlled environment during the casting process results in:
- Fewer Defects: The smooth flow of molten metal reduces the occurrence of defects like cold shuts and porosity.
- Dimensional Accuracy: High precision molds ensure that products are manufactured to exact specifications.
- Improved Surface Finish: The method often results in better surface finishes, reducing the need for extensive post-processing.
Reduced Waste and Efficient Resource Use
Low pressure casting significantly minimizes material waste. The controlled conditions of the process allow for:
- Optimal Metal Usage: With minimal overflow and spillage, businesses can reduce the amount of raw materials consumed.
- Recyclable Materials: Any scrap material generated can often be melted and reused, promoting sustainability.
Flexibility in Design
This casting method allows for a greater degree of design flexibility, essential in today’s fast-paced business environment. Designers can:
- Create Complex Geometries: Low pressure casting can produce intricate designs that might be challenging or cost-prohibitive with other methods.
- Utilize Various Materials: This technique supports the use of different metal alloys, catering to diverse industry requirements.
The Role of Low Pressure Casting in Various Industries
1. Art Supplies
In the world of art supplies, low pressure casting plays a pivotal role in creating high-quality sculptural elements, tools, and unique artistic pieces. Artists benefit from the precise and durable components produced through this method, enabling them to focus on their creative visions without worrying about the reliability of their materials.
2. Product Design
For product designers, the advantages of low pressure casting are manifold. The ability to produce custom metal parts swiftly and accurately makes it an invaluable tool in the prototyping phase. Designers can:
- Quickly Iterate Designs: Rapid prototyping becomes feasible, allowing for quicker testing and feedback loops.
- Enhance Functionality: The precision offered by low pressure casting means that functional aspects can be integrated into designs without compromising aesthetics.
3. 3D Printing
In the realm of 3D printing, low pressure casting serves as a complementary technology. It allows for:
- Material Diversity: 3D printed molds can easily be filled using low pressure casting, taking advantage of the rapid design capabilities of additive manufacturing.
- High-Volume Production: Once a design is validated, scaling up production using low pressure casting becomes a streamlined operation.
Case Studies: Successful Implementations
Case Study 1: Sculptural Art Installations
A local artist in the Midwest utilized low pressure casting to produce a series of sculptures that captured the intricate details of nature. The artist reported that the ability to control metal flow allowed for the creation of textures that were impossible with traditional methods. The durability of the sculptures also ensured that they could withstand outdoor conditions while maintaining their aesthetic appeal.
Case Study 2: Innovative Product Design in Electronics
A tech startup focused on designing consumer electronics experimented with low pressure casting for their product housings. By integrating low pressure casting into their production line, they reduced material waste by over 30% and significantly improved the robustness of their products. This led to enhanced customer satisfaction and market competitiveness.
Case Study 3: Collaborative 3D Printing with Low Pressure Casting
A leading industrial design firm adopted a two-pronged approach, leveraging 3D printing for rapid prototyping and low pressure casting for final production. By utilizing this combination, they substantially reduced lead times and improved their ability to pivot designs based on client feedback, ultimately leading to a more agile and responsive design process.
Conclusion: The Future of Low Pressure Casting
As the demand for high-quality, customizable products escalates, it is clear that low pressure casting will continue to play a vital role in various industries. Its benefits—ranging from enhanced product quality and reduced waste to design flexibility—make it an appealing choice for businesses looking to stay competitive in an increasingly demanding marketplace.
By embracing the advantages of low pressure casting, industries such as art supplies, product design, and 3D printing can elevate their processes and deliver superior products to their customers. If you are looking to incorporate low pressure casting into your business, consider consulting with experts who can guide you in implementing this efficient and effective manufacturing technique.
For more information on high-quality art supplies, innovative product design, and advanced 3D printing technologies, visit arti90.com, where we explore the intersection of creativity and technology.