The Evolution and Importance of China Plastic Injection Molds in Modern Business
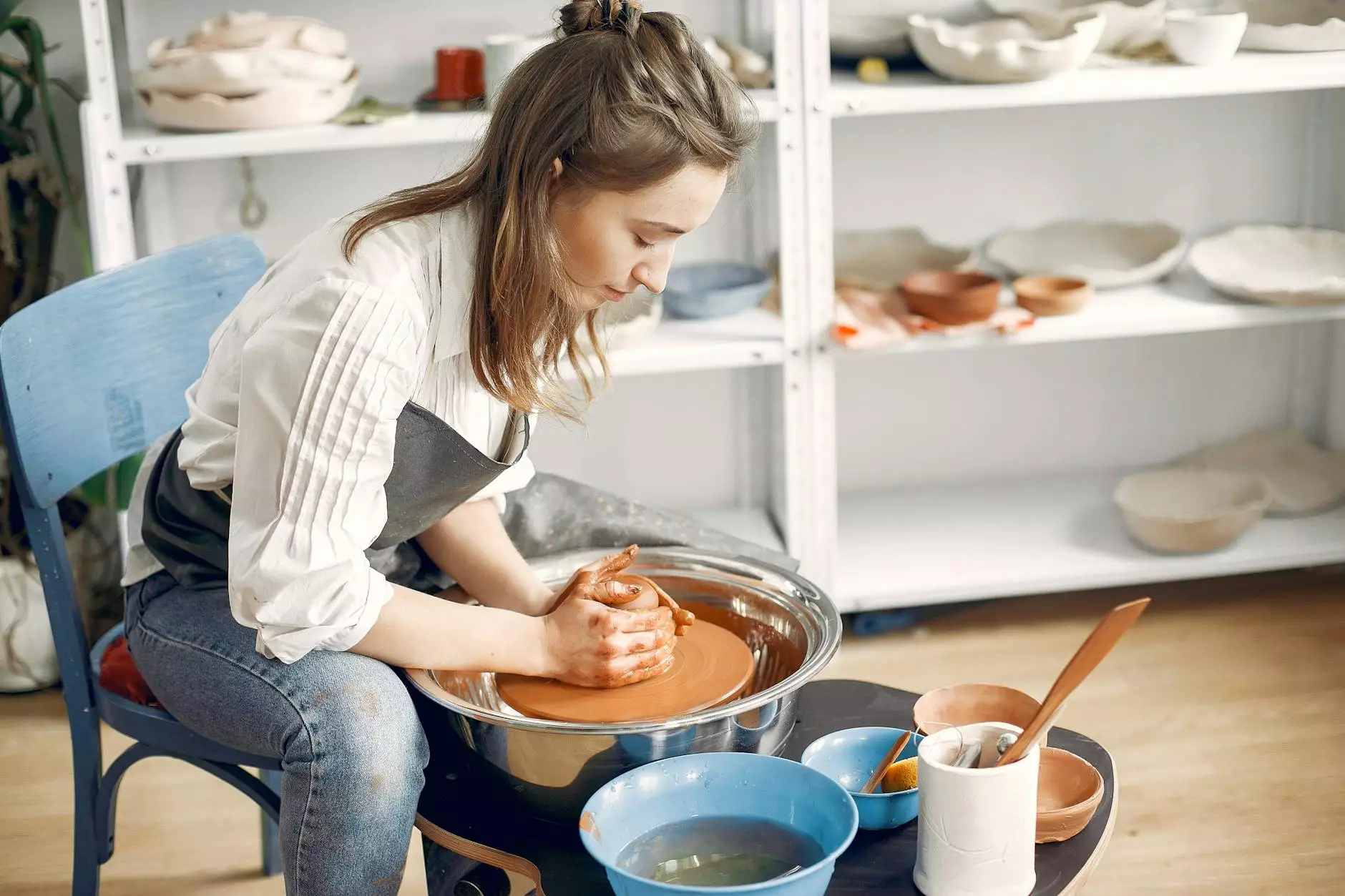
The world of manufacturing has undergone a radical transformation over the past few decades, particularly with the advent of advanced technologies. One of the most crucial advancements has been in the field of plastic injection molding. In this article, we will explore the significance of China plastic injection mold manufacturing, delve into its intricate processes, and discuss its pivotal role in modern business, particularly for industries such as metal fabrication.
Understanding Plastic Injection Molding
Plastic injection molding is a manufacturing process used to produce parts by injecting molten material into a mold. It is widely used for producing a variety of parts, from small components to large assemblies. The process starts with heating plastic resin until it becomes molten and then injecting it into a mold under high pressure. Once cooled, the final product is ejected from the mold, allowing for rapid production and consistent quality.
The Process and Benefits of Plastic Injection Molding
The plastic injection molding process involves several key steps:
- Material Selection: Different types of plastics can be used depending on the desired properties of the finished product. Common materials include ABS, polypropylene, and polyethylene.
- Mold Design: The design of the mold is critical; it determines the final product's shape and size. Advanced software tools are often used to create precise and efficient mold designs.
- Injection Phase: The selected plastic material is heated to a molten state and then injected into the mold cavity where it will cool and solidify.
- Cooling and Ejection: Once the plastic has solidified, the mold is opened and the finished part is ejected.
This process is incredibly efficient and can produce thousands of identical parts in a short amount of time, making it ideal for mass production. Additional benefits include:
- High Efficiency: The entire process can be completed in a matter of seconds or minutes, significantly reducing production time.
- Cost-Effectiveness: Once the molds are created, the cost per part tends to decrease with higher production volumes.
- Design Flexibility: Complex shapes and designs can be achieved that are often impossible with other manufacturing methods.
- Consistent Quality: Automated processes ensure high precision and uniformity across all parts.
The Role of China in Global Plastic Injection Mold Manufacturing
China has emerged as a powerhouse in the field of plastic injection molding. The country is home to a vast number of manufacturers specializing in the production of injection molds for various industries.
Advantages of Sourcing from China
Several factors contribute to China's dominant position in plastic injection mold manufacturing:
- Cost-Effective Production: The lower labor costs in China allow manufacturers to offer highly competitive prices, making it a popular choice for businesses worldwide.
- Advanced Technology: Many Chinese manufacturers have invested heavily in advanced technology and equipment, enabling them to produce high-quality molds that meet international standards.
- Skilled Workforce: The country has a substantial pool of skilled engineers and technicians specializing in mold design and manufacturing.
- Quick Turnaround Times: The ability to rapidly produce molds and components means businesses can respond quickly to market demands.
Applications of China Plastic Injection Molds
Plastic injection molds have a wide range of applications across various industries. Some of the most notable sectors benefiting from this technology include:
1. Automotive Industry
In the automotive sector, precision and reliability are paramount. China plastic injection molds are extensively used for producing components like:
- Dashboards
- Bumpers
- Consoles
- Light covers
These components not only need to fit together seamlessly but also must withstand rigorous testing for safety and performance.
2. Consumer Electronics
The consumer electronics market requires intricate designs for devices that are both functional and appealing. Plastic injection molds are used to produce parts of:
- Smartphones
- Laptops
- Wearable devices
The ability to create complex geometries in a cost-effective manner makes injection molding a preferred method for manufacturers.
3. Household Appliances
Appliances such as kitchen gadgets, vacuum cleaners, and washing machines benefit from the durability and versatility of molded plastic parts. Common uses include:
- Casings
- Buttons
- Internal components
In this sector, the appearance and functionality of the central components are critical for customer satisfaction.
Challenges in the Plastic Injection Mold Industry
Despite its many advantages, the industry faces multiple challenges that manufacturers must navigate:
Quality Control
Ensuring the quality of molds and components is essential. Poor quality can lead to defects and increased costs. Therefore, manufacturers need rigorous testing protocols in place.
Environmental Concerns
Plastic pollution is an ever-growing concern. Eco-friendly practices and materials are becoming increasingly important, requiring manufacturers to innovate continuously.
Intellectual Property Risks
As production shifts to countries like China, concerns over intellectual property theft and counterfeit products have grown. Companies need to implement protective measures and work with trusted manufacturers.
The Future of Plastic Injection Molding
The future of plastic injection molding looks promising with several trends shaping its evolution:
Increased Automation
The integration of robotics and automation technology will further increase efficiency and reduce labor costs in the manufacturing process.
Advanced Materials
Research into biodegradable and recyclable materials is likely to lead to new applications for plastic injection molding that are both sustainable and effective.
Digital Transformation
With the rise of Industry 4.0, companies are beginning to use data analytics and IoT technologies to enhance the efficiency of production processes. This transformation will lead to more responsive and optimized manufacturing environments.
Conclusion
The significance of China plastic injection mold manufacturing cannot be overstated. It plays a crucial role in various industries, offering innovative solutions that meet the demands of modern production. As we move forward, embracing challenges and leveraging opportunities will be essential for manufacturers to stay ahead in this competitive landscape. Businesses looking to enhance their production capabilities should consider the immense potential of plastic injection molding, especially when sourced from experienced and reliable manufacturers in China.
For further information on high-quality plastic injection molds and to explore how our capabilities can meet your manufacturing needs, visit deepmould.net.